Materials in Extreme Dynamic Environments (MEDE) [2015]
Composites: S-2 Glass/Epoxy Interface
Composite materials subjected to dynamic loads are essential examples of high performance systems in the conventional sense. In order to focus on the complexities raised by the interfaces and architectures, S-2 Glass/Epoxy is the model system for the Composites CMRG. The Composites CMRG develops the fundamental understanding of the role of interfaces, component interactions, and composite architecture over the full range of length scales and time scales that are manifested in the system during the dynamic event.
Application: S-2 Glass/Epoxy provides a strong, structural backing system to support protective plates for military vehicles. |
Composites Research Summary: Fiber-Matrix Interphase by Design
Professor Bazle Haque University of Delaware |
Professor John W. Gillespie, Jr. University of Delaware |
The fiber-matrix interphase plays a critical role in stress wave propagation, load transfer, and energy dissipation during micro-mechanical fiber fracture, interphase debonding, and matrix-cracking under extreme dynamic loading conditions. Molecular dynamics (MD) models of glass-fibers (SiO2), interphase sizing compound (GPS silane & epoxy), and the epoxy-amine matrix network have been developed to predict the rate-dependent properties and to understand the failure behavior of these constituent materials. The chemical composition and network structure of the interphase material greatly affects the chemical bonding to the glass surface and to the epoxy-amine matrix network. Figure 1 shows MD simulations of the fiber-matrix interphase. Such models have been subjected to dynamic loading under Mode I, Mode II, and Mixed-mode loading conditions to quantify the traction-separation behavior of the interphase. This has also been used to determine the parameters of a potential-based cohesive zone model (PPR-CZM), which is used at the next scale up. A high-strain-rate micro-droplet interphase test method has also been developed, and different fiber-matrix interphases have been characterized at a wide range of strain rates from near quasi-static to high strain-rates (up to 108 s-1). Finite element models of the dynamic micro- droplet experiments have been developed and simulated to determine a unique cohesive zone model (CZM) based on initiation and propagation of a crack in the fiber-matrix interphase. We expect that our MD predictions of the parameters of the potential based interphase traction-separation behavior will enable the design of a fiber-matrix interphase for optimum energy dissipation under extreme dynamic loading condition.
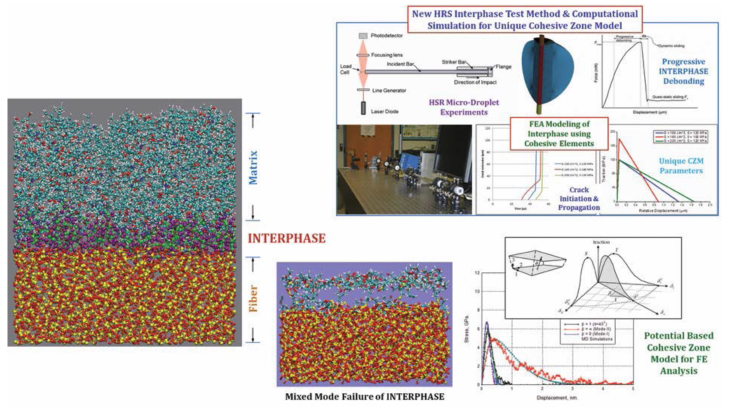
Figure 1: Methodology for Composites Fiber-Matrix Interphase by Design.
Polymers: UHMWPE
Polyethylene is the model system for the Polymers CMRG because of the potential for significant improvement in its mechanical properties. Ultra High Molecular Weight Polyethylene (UHMWPE) is used in a wide variety of military applications in both tape and fiber forms, but its tensile strength remains an order of magnitude below the theoretical value. The Polymers CMRG seeks to determine the roles of atomic scale defects, chain length, degree and length scale of crystallinity in determining and limiting the mechanical response under extreme dynamic conditions.
Application: UHMWPE shows tremendous promise for the next generation of helmets and body protection for soldiers. |
Polymers Research Summary: Dynamic Mechanical Behavior of Single Ballistic Fibers
Professor Wayne Chen Purdue University |
Professor Joseph Deitzel University of Delaware |
Dr. Daniel Casem Army Research Laboratory |
In this research effort, the mechanical response of single filaments of high-performance fibers, including Spectra®100d and 13d have been determined under uniaxial tension, tension/shear, and transverse compression loading conditions with loading rates varying from quasi-static to dynamic. Single fibers are subjected to various known levels of both torsional shear strain and axial tensile stress to determine the effects of combined loading on the tensile strength. Axial tension experiments are performed on pre-twisted fibers using a miniature tension
Kolsky bar and MTS servo-hydraulic system. The resulting torque generated by fibers loaded to specific degrees of shear strain is determined using an in-house developed torque sensing technique. Compilation of the two stress states has generated a biaxial failure surface criterion yielding the residual tensile strength of single fibers when subjected to a specific level of shear stress. To study the fiber response under transverse compression, we use an improved method for fiber transverse compression developed previously. Two fiber specimens are laid parallel and compressed between two tool steel platens to obtain the nominal stress–strain curves under quasi-static loading. To evaluate the rate effects on the transverse behavior, high-rate transverse compression experiments are performed at ARL using a miniature Kolsky bar.
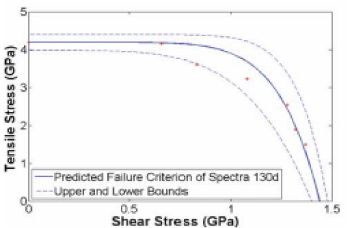
Figure 2: Bi-axial failure surface of Spectra® 130d.
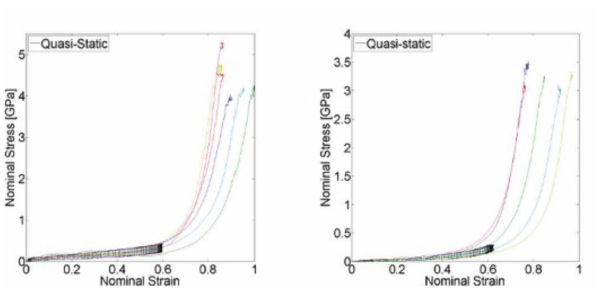
Figure 3: Dynamic transverse compressive response of Kevlar (left) and Dyneema (right) single fibers
(the data below 0.6 strain with error bands are quasi-static results)..