
|
![]() |
Under the Defense Advanced Research Projects Agency (DARPA) Tailorable Feedstock for Forming (TFF) program, the University of Delaware – Center for Composite Materials led-team proposed to develop a manufacturing process and pilot facility to produce novel discontinuous carbon fiber composite feedstock for forming, with the potential to revolutionize the use of composite materials, as a cost-effective replacement for small complex geometry metal parts (‹sq. m.)
The TuFF (Tailored Universal Feedstock for Forming) feedstock consists of a highly aligned discontinuous carbon fiber preform in thin-ply format, which can be combined with thermoplastic or thermoset resins for prepreg, or used in dry form for infusion-based manufacturing processes. A patented discontinuous fiber alignment and preforming process has been developed and implemented in a pilot facility at UD-CCM. The alignment process is fiber agnostic and TuFF preforms have been manufactured with aerospace grade fiber (IM7, T800), pitch carbon fiber, and recycled carbon fiber. Using discontinuous IM7 carbon fiber and Polyetherimide (PEI) thermoplastic resin, TuFF composites with aerospace quality requirements (‹1% voids, up to 63% fiber volume fraction) have demonstrated 100% translation of fiber stiffness and strength in tension, and >40% bi-axial in-plane strain capability during forming. The in-plane stretchability of TuFF preforms enables conformability of simple planar preforms to complex geometries, eliminating the need for darting and complex ply patterns while minimizing associated scrap during composite layup. Closed-loop recycling and reuse strategies are possible for the first time with the ability to reuse fiber and preform scrap, prepreg scrap and recycled composite parts. |
• World’s Strongest Short Fiber Composite • Low Pressure 40% Bi-Axial Stretch Formable • Fiber and Resign Agnostic • Closed Loop, Zero Waste Production • Fully Recyclable Material • Thin Ply Formats Available • Steerable Tape ![]() 250gsm quasi-isotropic [0/90/45/-45]s laminate |
The Tailorable Universal Feedstock for Forming (TuFF) material is comprised of highly aligned discontinuous fibers achieves a high level of mechanical properties with large in-plane extensibility for forming of complex geometries. The TuFF microstructure has been characterized in terms of areal weight and fiber volume fraction uniformity and statistical distributions of fiber length, fiber-fiber spacing and fiber alignment using microscopy and Computer-Tomography [Ref 1].
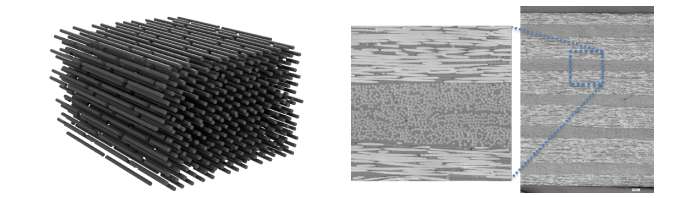
A critical material parameter is the fiber length and aspect ratio. Fiber length can be controlled via the cutting process and IM7 fiber in the mm-range with an aspect ratio of more than 600 (>3 mm length) provides full property translation and excellent formability. A wide range of fiber lengths can be aligned with no or limited fiber breakage occurring throughout the alignment process.
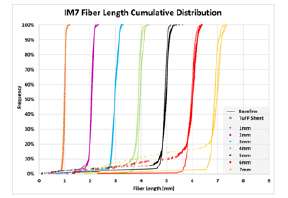
Fiber orientation is the key parameter to evaluate alignment quality. Computer Tomography (CT) can be used to evaluate the TuFF 3D-volume. Data was generated and the alignment for multiple samples based on the algorithm developed at the Army Research Laboratory is compared to continuous fiber sample [Ref 2] as well as literature data from a competing short fiber alignment process [Ref 3]. The alignment orientation is very repeatable as sample-to-sample variation is low and approaches continuous fiber prepreg quality with more than 98% of all fibers aligned within 10 degrees.
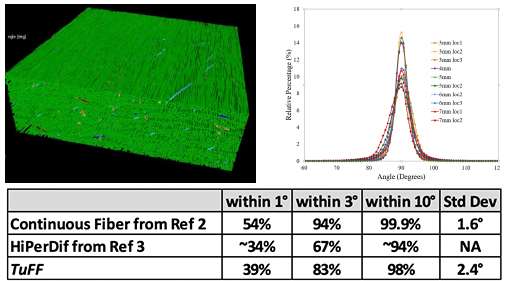
References:
1) Dirk Heider, John Tierney, Mohamed A. Henchir, Verena Gargitter, Shridhar Yarlagadda, John W. Gillespie, Jr., Jessica Sun, Jennifer M. Sietins, Dan Knorr, “Microstructural Evaluation of Aligned, Short Fiber TuFF Material,” SAMPE Conference Proceedings. Charlotte, NC, May 20-23, 2019.
2) Andrew L. Stewart, Anoush Poursartip, “Characterization of fibre alignment in as-received aerospace grade unidirectional prepreg”, Composites Part A 112 (2018) 239–249.
3) H. Yu, K.D. Potter, M.R. Wisnom, ” A novel manufacturing method for aligned discontinuous fibre composites (High Performance-Discontinuous Fibre method)”, Composites: Part A 65 (2014) 175–185.
Discontinuous fiber composites can alleviate manufacturing challenges by enabling sheet metal like processing [1] and reduce cost with the use of lower cost fiber feedstock, especially with the increase in recycled carbon fiber (discontinuous) that is now available in the market [2]. The ideal discontinuous fiber microstructure is highly aligned with well-controlled fiber spacing in all three directions, which has been predicted to have properties equivalent to continuous fiber systems when the aspect ratio is sufficiently high (e.g. L/D ~1000). TuFF (Tailored Universal Feedstock for Forming) consists of a highly aligned discontinuous carbon fiber preform in thin-ply format, which can be combined with thermoplastic or thermoset resins to make high performance composites. Using discontinuous IM7 carbon fiber (3mm) and Polyetherimide (PEI) thermoplastic resin, TuFF composites with aerospace quality requirements (<1% voids, up to 63% fiber volume fraction) have demonstrated equivalent properties to date, with comparable continuous fiber systems. High quality composite laminates were fabricated with from highly-aligned discontinuous fiber preforms comprised of 3 mm IM7 fibers and PEI Film, for tension, compression, short beam shear and quasi-isotropic tension performance assessment. Panels were fabricated in the autoclave to ASTM test dimensions with Fiber Volume Fractions of ~58% nominal, and ultrasonically scanned prior to testing. Test results are shown in the Table below for the various panels tested to date. TuFF composite laminates with 3mm IM7 fibers are also being fabricated and tested with PEKK and 8552 epoxy. |
Comparison of TuFF tension properties to short fiber composites in Literature. Note that Literature data includes Standard Modulus carbon fiber compared to IM fibers in TuFF
|
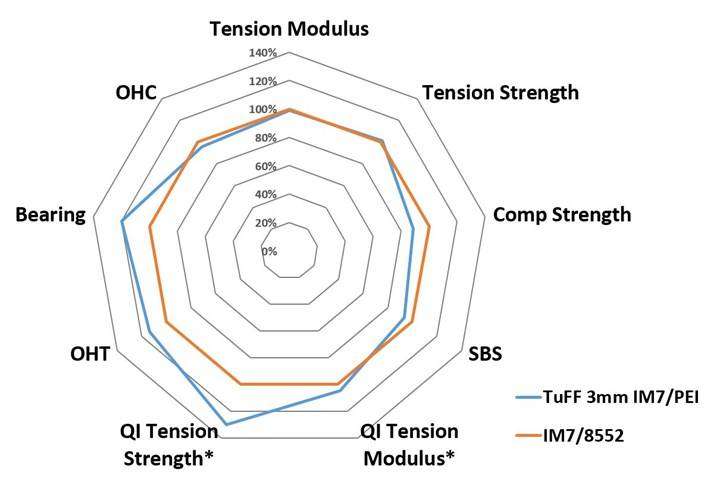
[2] Internal testing of IM7/8552 Experimental Grade 70 gsm thin-ply prepreg
The TuFF (Tailored Universal Feedstock for Forming) feedstock consists of a highly aligned discontinuous carbon fiber preform in thin-ply format, which can be converted to dry preforms for thermoset infusion, thermoset prepreg blanks or thermoplastic blanks for composite forming. TuFF microstructure enables sheet-metal like formability due to highly homogenous microstructure and control of fiber length. Fiber length measurements show low variability with 90% of the fibers within 2.8-3.2 mm with an average fiber length of 3.0 mm for IM7 carbon fiber (L/D of ~600). The uniformity in length in conjunction with the short fiber length (i.e. 3mm) enables significantly more complicated geometric features to be formed with lower effective viscosities which is proportional to (L/D)2.
Forming demonstrations have shown metal-like formability for complex geometries. In-plane as well as bi-axial stretch >40% has been demonstrated in both longitudinal (along fiber direction) and transverse (90 degrees to fiber direction) deformation modes for unidirectional composite blanks. Complex geometry demonstrations include a sine wave (23% and 40% strain), a waffle with a corrugated geometry (30% strain in each cell) and a challenge part with two pockets (40% strain along direction with both pockets and 30% strain in transverse direction). In all cases, the forming process was performed with constrained boundaries and photographs show the formed blanks as-is with no trim, reflecting true in-plane stretch during the forming process.
Insert | Laminate | Part Formed with Constrained Boundary | Observations |
Flattened Bead | 3mm IM7 PEI [0]28 57% FVF |
![]() |
42% Strain in fiber direction with no evidence of fiber pull-in at edges or failure (gaps or extreme thinning) |
Flattened Bead | 3mm IM7 PEI [90]28 52% FVF |
![]() |
42% Strain transverse to fiber direction with no evidence of transverse splitting. Small pull-in at bead location in fiber direction led to improved edge clamping |
Sine Wave | 3mm IM7 PEI [0/90]s 54% FVF |
![]() |
Both Sine Waves (23% to 40%) formed well, no splitting or thinned regions, boundary unchanged |
“Waffle” | 3mm IM7 PEI [0/90]s 54% FVF |
![]() |
Uniform deformation in each cell of the “waffle”. 30% local strain in each cell |
Challenge Part | 3mm IM7 PEI [0/90]s 54% FVF |
![]() |
Total 40% strain along both pockets, 30% at larger pocket. Some uniform thinning at bottom of large pocket |
Current Carbon (CF) Fiber Reinforced Polymers (CFRP) recycling strategies reclaim continuous CF in powder or short fiber form. The material is added to molding compounds as a filler or short fiber reinforcement having random or semi-aligned orientation to produce composites with low fiber volume fraction and reduced mechanical properties (down cycling). Down cycling reduces the value chain limiting the recycling opportunities of CFRPs. In contrast our short fiber alignment process (TuFF) allows 1) the use of low-cost, short CFs obtained from recycled and waste stream, and 2) recycling of TuFF material using thermolysis to produce highly aligned short fiber composites with mechanical properties approaching continuous fiber levels. The closed-loop process recycles the CFRP, reclaims the fiber content, aligns the fibers using the TuFF process and produces new CFRP components with high property retention. The method reduces material and part cost and allows true recycling and reuse of CF components into high-performance parts.Recycling with 100% property retention of carbon composites made from Arkema Elium resin and IM7 carbon fiber has been demonstrated. A low-temperature pyrolysis process was used to remove the polymer content and did not show significant degradation of the fiber length. The TuFF short fiber alignment process was used to process the recycled carbon fiber and showed full mechanical property retention. The closed-loop process recycles the composite, reclaims the fiber content, aligns the fibers using the TuFF process and produces new composite components with equivalent mechanical properties. The method reduces material and part cost and allows true recycling and reuse of carbon fiber components into high-performance parts.
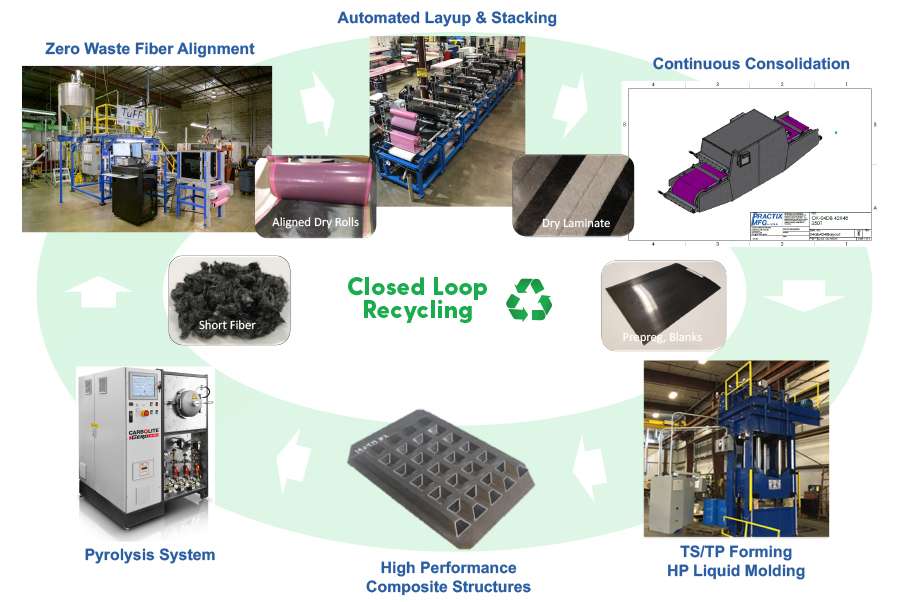
5 Ton TuFF Production Facility • Automated 5 Ton Low Cost Facility • Zero waste non-toxic process • Ability to produce off-axis plies with in-line stacking • Easily scalable facility Production |
November 2022 | U.S Air Force awards $13.5M to UD-CCM “I am really excited at the opportunity to mature the TuFF pre-pregging process and demonstrate high-throughput composite thermoforming for Air Force relevant components,” said David Simone of the U.S. Air Force. Read MoreMarch 2021 | NASA provides $45 million boost to U.S. small businesses “At NASA, we recognize that small businesses are facing unprecedented challenges due to the pandemic,” says Jim Reuter, associate administrator for the agency’s Space Technology Mission Directorate (STMD). Read More March 2021 | University of Delaware TuFF composite material shows high potential for UAM |
![]() |
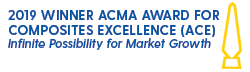
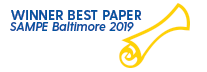
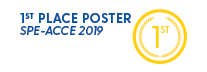
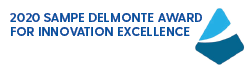